Oracle ASCP Training
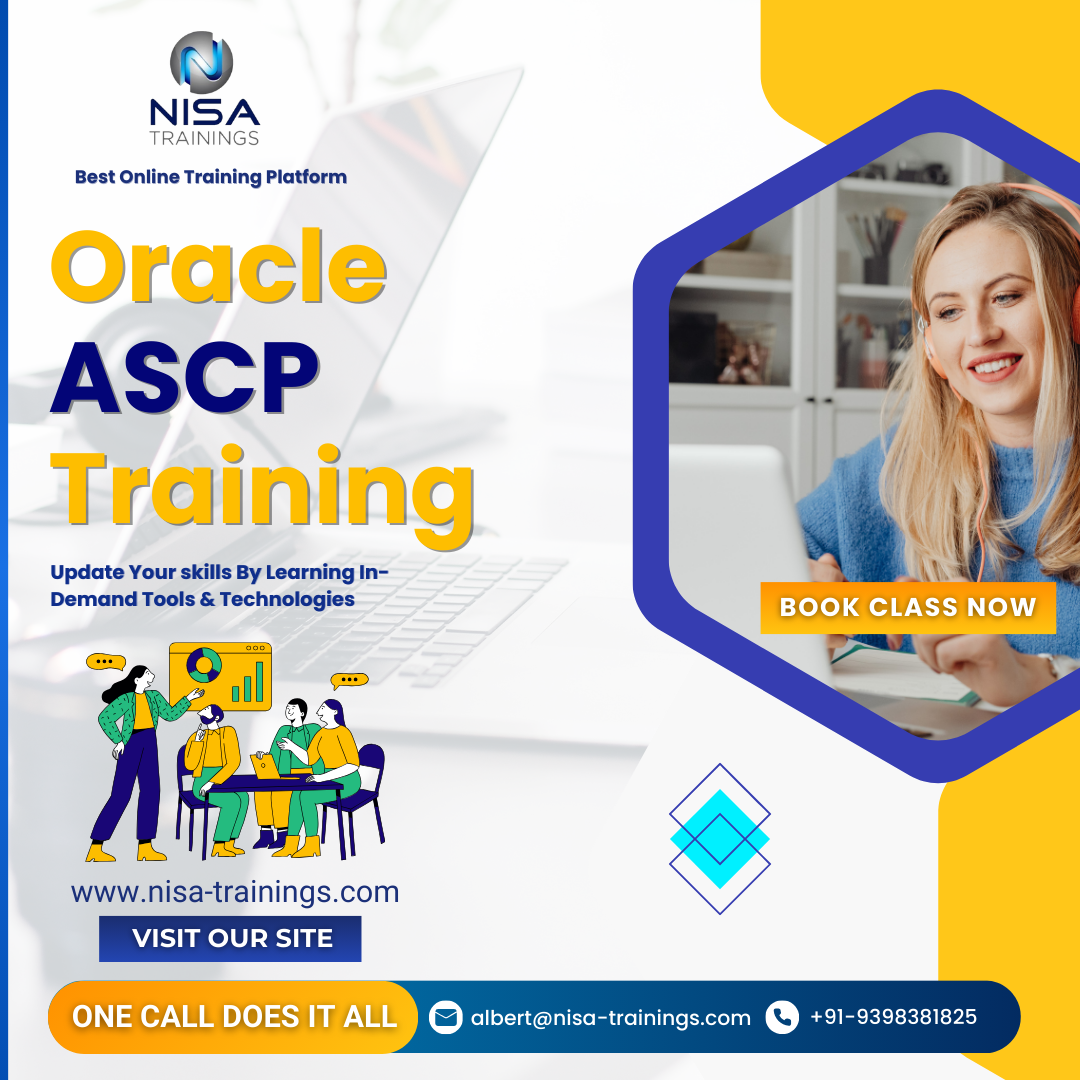
Why should you choose Nisa For Oracle ASCP Training?
Nisa Trainings is the best online training platform for conducting one-on-one interactive live sessions with a 1:1 student-teacher ratio. You can gain hands-on experience by working on near-real-time projects under the guidance of our experienced faculty. We support you even after the completion of the course and happy to clarify your doubts anytime. Our teaching style at Nisa Trainings is entirely hands-on. You’ll have access to our desktop screen and will be actively conducting hands-on labs on your desktop.
Job Assistance
If you face any problem while working on Oracle ASCP Course, then Nisa Trainings is simply a Call/Text/Email away to assist you. We offer Online Job Support for professionals to assist them and to solve their problems in real-time.
The Process we follow for our Online Job Support Service:
- We receive your inquiry for Online Job
- We will arrange a telephone call with our consultant to grasp your complete requirement and the tools you’re
- If our consultant is 100% confident in taking up your requirement and when you are also comfortable with our consultant, we will only agree to provide service. And then you have to make the payment to get the service from
- We will fix the timing for Online Job Support as mutually agreed by you and our consultant.
Course Information
Oracle ASCP Training
Duration: 25 Hours
Timings: Weekdays (1-2 Hours per day) [OR] Weekends (2-3 Hours per day)
Training Method: Instructor Led Online One-on-One Live Interactive
Sessions.
COURSE CONTENT :
Module 1: Introduction to Oracle ASCP
Overview of Supply Chain Management (SCM)
- Understanding the Oracle SCM Suite
- Role of ASCP in the Oracle Supply Chain
- Key Features and Benefits of ASCP
- ASCP Architecture and Components
Overview of Advanced Supply Chain Planning
- Importance of supply chain planning in modern businesses
- ASCP’s role in managing demand and supply across the supply chain
- Integration with other Oracle modules (e.g., Inventory, Manufacturing, Purchasing, Order Management)
Module 2: Configuring Oracle ASCP
ASCP Setup and Configuration
- Defining and setting up planning organizations
- Configuring ASCP parameters and planning data sources
- Setting up planning calendars, shifts, and resources
Supply Chain Models
- Defining supply chain models in ASCP
- Setting up inventory and distribution networks
- Integrating with Oracle Inventory and Manufacturing
Planning Strategies Configuration
- Configuring planning strategies: Make-to-Stock (MTS), Make-to-Order (MTO), Engineer-to-Order (ETO)
- Setting up planning rules (e.g., safety stock, lead time, lot sizing)
Module 3: Demand Planning
Forecasting Demand
- Overview of demand forecasting in ASCP
- Integrating historical demand data
- Analyzing demand patterns and trends
Demand Management
- Setting up demand types and models
- Managing sales orders and forecasted demand
- Handling demand changes and adjustments
Collaborative Demand Planning
- Working with external partners and customers for demand collaboration
- Handling forecast consumption and demand reconciliation
Module 4: Supply Planning
Supply and Demand Balancing
- Generating supply plans based on forecasted demand
- Reconciling supply and demand to avoid shortages or excess inventory
- Defining global supply plans vs local plans
Supply Planning Strategies
- Managing material shortages, production delays, and supply constraints
- Procurement and production planning for materials and components
Planning and Procurement Integration
- Integrating supply planning with Oracle Purchasing and Oracle Inventory
- Handling purchase requisitions and supplier collaboration
Module 5: Capacity Planning
Capacity and Resource Constraints
- Understanding capacity planning in ASCP
- Managing machine, labor, and other resource constraints
- Setting up work centers, routings, and resource availability
Finite Capacity Scheduling
- Managing finite scheduling and optimizing resource utilization
- Defining work center capacities and constraints
- Scheduling production with capacity constraints
Capacity Management and Optimization
- Analyzing resource capacity and balancing workloads
- Using ASCP’s capacity planning reports and dashboards
Module 6: ASCP Planning Runs
Running Planning Processes
- Introduction to ASCP planning runs
- Configuring planning options and running the planning process
- Generating supply and demand plans with ASCP
Plan Generation
- Setting up plan types (e.g., Global, Local)
- Running supply/demand balancing
- Generating production and procurement schedules
Plan Revisions and Adjustments
- Reviewing and analyzing planning results
- Adjusting plans based on capacity, demand, or other factors
- Managing exceptions and making adjustments to the plan
Module 7: Monitoring and Analyzing Plans
Analyzing Plan Results
- Using the Supply/Demand Workbench
- Identifying and resolving plan issues and exceptions
- Analyzing key metrics for supply chain performance
Exceptions Management
- Handling unfulfilled demand, late deliveries, and supply shortages
- Using alerts and notifications for exceptions
Reports and Dashboards
- Using standard ASCP reports (e.g., supply/demand reports, shortage reports)
- Customizing reports and creating new ones based on planning data
- Using dashboards to track real-time performance and KPIs
Module 8: Integration with Other Oracle Applications
Integration with Oracle Inventory and Manufacturing
- Managing stock levels with Oracle Inventory
- Synchronizing manufacturing orders and production plans with Oracle Manufacturing
Integration with Oracle Purchasing
- Aligning procurement plans with supply chain plans
- Managing purchase orders, suppliers, and material replenishment
Integration with Oracle Order Management
- Handling sales orders and integrating with demand planning
- Managing order fulfillment and inventory
Data Synchronization
- Understanding how data is shared and synchronized between Oracle ASCP and other modules
- Integration with external systems or third-party applications
Module 9: Advanced ASCP Features and Best Practices
Scenario Planning and “What-If” Analysis
- Running different scenarios to evaluate potential planning outcomes
- Managing risk and uncertainty with scenario planning
Optimization and Cost Minimization
- Using ASCP optimization tools to reduce costs (e.g., minimizing transportation costs, optimizing inventory)
Advanced Planning Techniques
- Working with mixed-mode planning and advanced scheduling
- Fine-tuning parameters to optimize production schedules and inventory levels
Best Practices for ASCP Implementation
- Tips for successfully implementing and configuring ASCP in your organization
- Common pitfalls and challenges to avoid during implementation
Module 10: Troubleshooting and Maintenance
Troubleshooting Common Issues
- Handling errors in plan generation, resource allocation, and demand-supply balancing
- Resolving data discrepancies and planning inconsistencies
System Maintenance and Updates
- Regular maintenance tasks for ASCP (e.g., updates, patching)
- Managing system performance and scalability