Accuplus 3PL WMS training
Accuplus 3PL WMS training course is designed to equip users with the knowledge and skills required to effectively operate the Warehouse Management System (WMS) for third-party logistics (3PL) operations. The course content typically focuses on mastering key functionalities of the software, optimizing warehouse operations, and ensuring smooth order fulfillment and inventory management.
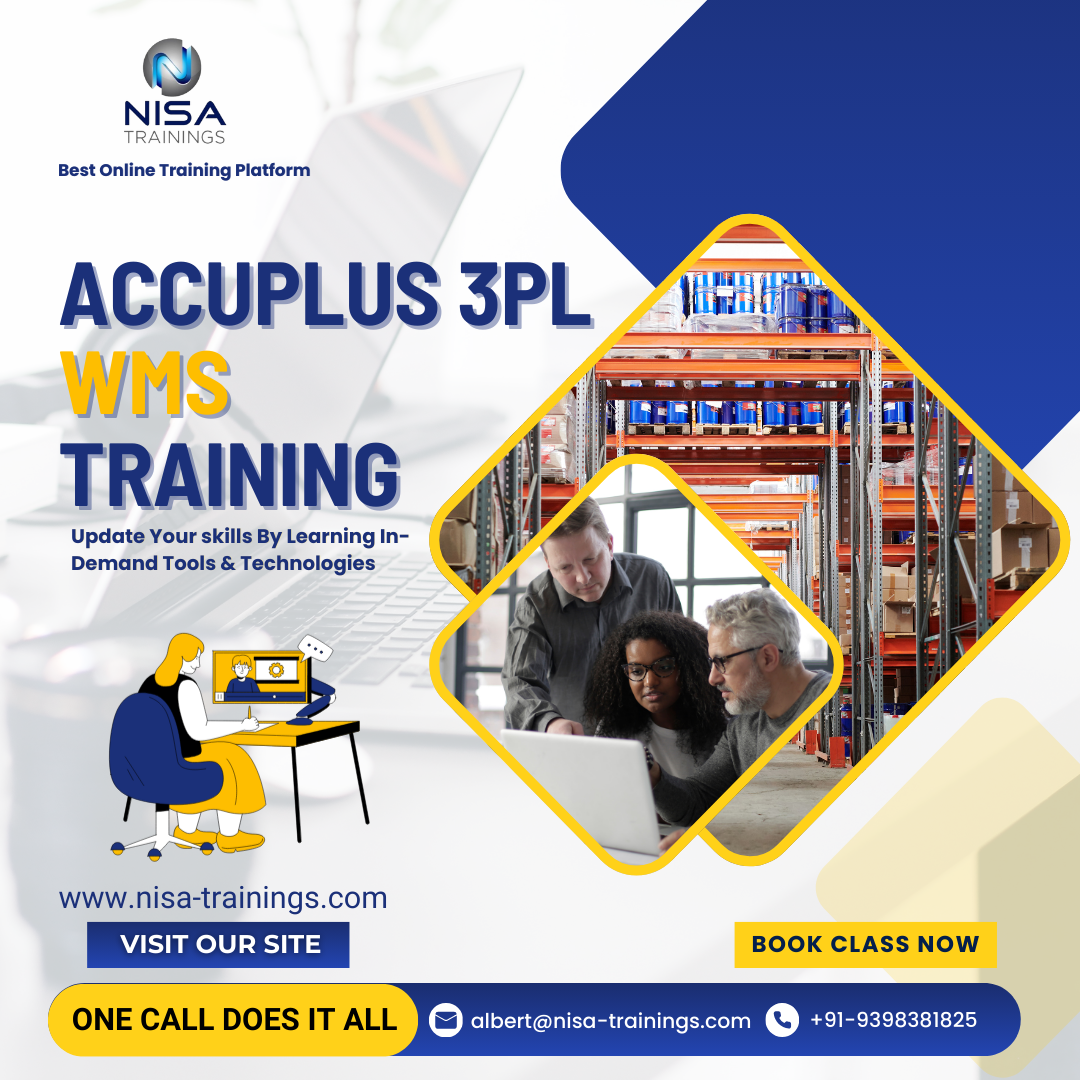
Why should you choose Nisa For Accuplus 3PL WMS Training?
Nisa Trainings is the best online training platform for conducting one-on-one interactive live sessions with a 1:1 student-teacher ratio. You can gain hands-on experience by working on near-real-time projects under the guidance of our experienced faculty. We support you even after the completion of the course and happy to clarify your doubts anytime. Our teaching style at Nisa Trainings is entirely hands-on. You’ll have access to our desktop screen and will be actively conducting hands-on labs on your desktop.
Job Assistance
If you face any problem while working on Accuplus 3PL WMS Course, then Nisa Trainings is simply a Call/Text/Email away to assist you. We offer Online Job Support for professionals to assist them and to solve their problems in real-time.
The Process we follow for our Online Job Support Service:
- We receive your inquiry for Online Job
- We will arrange a telephone call with our consultant to grasp your complete requirement and the tools you’re
- If our consultant is 100% confident in taking up your requirement and when you are also comfortable with our consultant, we will only agree to provide service. And then you have to make the payment to get the service from
- We will fix the timing for Online Job Support as mutually agreed by you and our consultant.
Course Information
Accuplus 3PL WMS Training
Duration: 25 Hours
Timings: Weekdays (1-2 Hours per day) [OR] Weekends (2-3 Hours per day)
Training Method: Instructor Led Online One-on-One Live Interactive
Sessions.
COURSE CONTENT :
Module 1: Introduction to Accuplus 3PL WMS
- Overview of Accuplus 3PL WMS:
- Purpose and features of the WMS.
- How it fits into 3PL operations.
- System components: dashboard, user interface, and key modules.
- System Setup:
- Initial configuration and system integration.
- Defining business rules and preferences.
- Customizing the interface to suit operational needs.
Module 2: User Roles and Permissions
- User Roles:
- Overview of different roles (administrator, warehouse staff, manager, etc.).
- Creating and managing user profiles.
- Permissions:
- Setting access levels for different system features.
- Defining security protocols for user authentication.
Module 3: Inventory Management
- Inventory Tracking:
- Creating and managing inventory records.
- Stock movement and tracking via barcode scanning.
- Managing inventory locations (racking, shelving, etc.).
- Handling multiple inventory types and SKUs.
- Stock Receiving:
- Receiving inventory from suppliers.
- Data entry for received goods (using barcode scanners or manual entry).
- Updating stock levels and locations.
- Putaway Procedures:
- Storing goods in appropriate warehouse locations.
- Optimizing the putaway process for efficiency.
- Inventory Adjustments:
- Conducting stock counts (cycle counting, physical inventory).
- Making adjustments for discrepancies (damaged, lost, or missing items).
- Reconciliation of inventory errors.
Module 4: Order Management
- Order Processing:
- Receiving and managing orders in the system.
- Order entry (manual vs. automated data entry).
- Managing order priorities and statuses.
- Order Picking:
- Overview of picking methods (e.g., single, batch, zone picking).
- Picking strategies and optimizing workflows.
- Using mobile devices and barcode scanners to pick orders.
- Packing:
- Packing orders into boxes, containers, or pallets.
- Using packing materials efficiently.
- Generating packing slips and labels.
- Shipping:
- Generating shipping labels and integrating with carriers (UPS, FedEx, etc.).
- Tracking and updating shipment statuses.
- Handling shipment delays or issues.
- Returns Management:
- Managing returns from customers.
- Processing returned items and updating inventory.
Module 5: Advanced Inventory and Order Handling
- Backorders:
- Handling out-of-stock situations.
- Managing backorders and notifying customers.
- Batch and Expiry Tracking:
- Managing products with batch numbers and expiration dates.
- Performing FIFO (First In, First Out) or LIFO (Last In, First Out) inventory management.
- Multi-location and Multi-client Handling:
- Managing inventory across different locations or warehouses.
- Supporting multiple 3PL clients with distinct inventory requirements.
Module 6: Warehouse Operations Optimization
- Warehouse Layout Optimization:
- Best practices for organizing the warehouse for efficient operations.
- Strategic placement of high-demand items.
- Workflow Automation:
- Automating tasks such as order routing, picking, and packing.
- Integrating automated systems (conveyors, robots) with the WMS.
- Resource Management:
- Managing workforce allocation based on order volume.
- Tracking labor productivity and performance.
Module 7: Shipping & Distribution
- Carrier Integration:
- Integrating with shipping carriers for real-time rate quotes and label generation.
- Setting up routing guides for preferred carriers.
- Tracking shipments and managing shipping discrepancies.
- Shipping Rules and Compliance:
- Understanding and setting shipping policies (e.g., hazardous materials, international shipping).
- Creating compliant shipping labels and documentation.
Module 8: Reporting and Analytics
- Generating Reports:
- How to generate and interpret various warehouse reports (inventory, order history, shipping status, etc.).
- Customizing reports for different management levels (warehouse supervisor, operations manager, etc.).
- Key Performance Indicators (KPIs):
- Monitoring warehouse performance metrics (order accuracy, shipping times, inventory turnover).
- Using data to improve operational efficiency.
- Forecasting and Demand Planning:
- Leveraging historical data to predict demand and optimize stock levels.
Module 9: System Maintenance & Troubleshooting
- Regular System Maintenance:
- Software updates and upgrades.
- Performing backups and restoring data.
- Common System Errors:
- Troubleshooting common WMS errors (e.g., missing inventory, order mismatches).
- How to resolve issues related to order processing, inventory tracking, and system performance.
- Technical Support:
- Accessing customer support for advanced troubleshooting.
- Understanding when and how to escalate issues.